CASE STUDY: ChemGrout CG500 – Tahmoor Mine – Rock Bolting
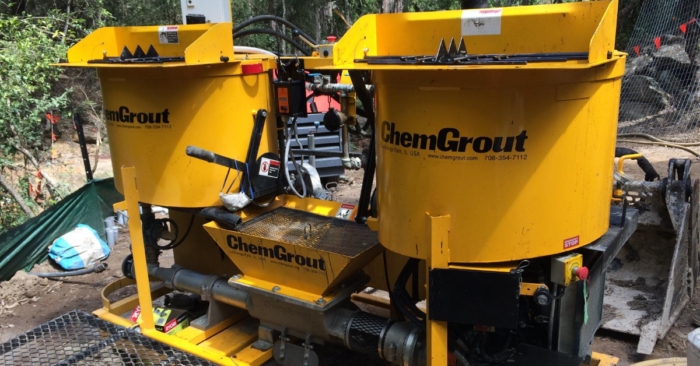
Grouting Precision for Rail Infrastructure: CGS Equipment Supports Tahmoor Mine Stabilisation Project
Objective: Rock Bolting Structural Reinforcement of Brick-Lined Culvert
The Tahmoor Coal Mine is located in the Southern Highlands of New South Wales, producing hard coking coal and a small amount of steaming blend coal for export to key markets in Europe and Asia. A historic brick-lined culvert, supporting a railway embankment, required rock bolting reinforcement to prevent ground subsidence during mining activities.
To safeguard the railway and ensure no disruption to mining activities, Glencore (the mine operator) approached CGS Equipment whilst developing a ground stabilisation strategy for the site. The location and nature of the mine site presented several challenges. In particular, the equipment solution had to deliver grout in hard-to-access locations and produce a high volume of output to reduce project length and any potential effect on the mining operations.
CGS Equipment’s Solution: ChemGrout CG500 Hydraulic Grout Pump
Based on Glencore’s requirements, CGS Equipment recommended the ChemGrout CG500 hydraulic grout pump. The grout plant delivered consistent, high-volume grout output and pumped this over a 55-metre horizontal distance to the required injection points.
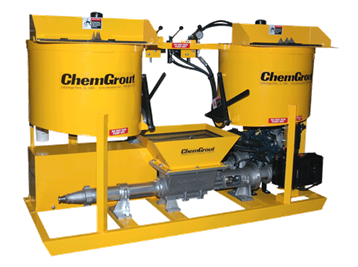
Key Benefits Delivered:
-
Variable Speed Control: The progressive cavity pump allowed for gradual pressure increases, avoiding material wastage and line blockages.
-
Efficient Mixing: The mix tank design with side baffles and reversible paddles ensured fast, uniform mixing, reducing labour hours.
-
Superior Mix Quality: Reversible paddles delivered minimal bleed and high-strength grout, ideal for structural bonding
Reliable Rock Bolting Grout Solutions from CGS Equipment
CGS Equipment provides high-performance grout pumps and mixers for mining, tunnelling, infrastructure, and civil projects across Australia. Review our grouting range here or contact one of our expert team today
1300 581 984
sales@cgsequipment.com.au