CASE STUDY: Cemen Tech Volumetric Concrete Mixer (Stationary)
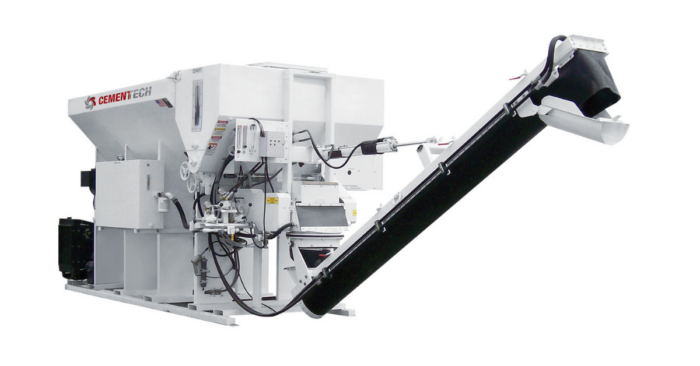
Project Overview: Precast Concrete Segments for Tunnel Lining
A customer contacted CGS Equipment seeking a customised solution for their unique project requirement. The customer needed to produce thousands of pre-cast concrete panels over a nine-month period. The requirement was clear: find a machine that delivers a cost-effective, highly accurate and consistent concrete solution. CGS Equipment identified a Cemen Tech volumetric concrete mixer as the optimal solution.
Choosing the Right Mixing Solution for Complex Production
Initially a conventional approach was considered – using multiple one-tonne pan mixers. While widely used in the refractory industry for low cement castable products, this method proved unsuitable for this project. The extensive crane movements required to feed raw materials, along with the difficulty in maintaining batch control, made this traditional solution inefficient and unreliable.
Instead, the project demanded a mixing system capable of delivering precise and consistent results for every single panel. As quality control was paramount, the ability to closely monitor the ratio of cement, aggregates, and water throughout the production process was essential. A volumetric concrete mixer gives the operator complete control over mix designs and the ability to develop precise recipes based on the desired outcome.

Introducing the solution: Cemen Tech’s Volumetric Concrete Mixer – SCD5-100
A Cemen Tech SCD5-100 was installed at the manufacturing facility. Sand, stone and cement were delivered in bulk and loaded directly into the mixer. A custom conveying system was developed to streamline workflow and move the moulds to a finishing station.
The integrated computer system, known as AP2, enabled the production team to track key metrics such as mix volume and raw material usage. Data was exported via USB, providing full transparency and quality control reporting.
Initial test runs were crucial to fine-tuning the mix design. These trials allowed precise calibration of stone gates, cement ratios, and water flow. Once the ideal mix design was established, settings required minimal adjustment. Sample moulds produced during testing were cured, cored, and analysed to verify compliance with design specifications.

Performance of the Volumetric Concrete Mixer
Deploying the Cemen Tech SCD5-100 eliminated delays associated with traditional ready-mix concrete deliveries. Continuous casting of concrete was undertaken six days a week for nine months. The ‘on-demand’ production ability significantly reduced waste and labour costs. The team completed the work four months ahead of schedule despite the project’s initial timeline being shortened by three months.
Thanks to the precision and consistency offered by the Cemen Tech volumetric concrete mixer, only 0.006% of panels did not meet the strict quality assurance criteria. This exceptional result underscores the reliability and efficiency of the Cemen Tech SCD5-100 and highlights CGS Equipment’s commitment to delivering high-performance concrete solutions, tailored to your project.
For contractors and project managers looking to streamline concrete operations with minimal waste and maximum precision, CGS Equipment’s expertise and the Cemen Tech SCD5-100 offer a proven path to success
Explore our range of volumetric concrete mixers, or speak to one of our friendly team today.
1300 581 984
sales@cgsequipment.com.au