CASE STUDY: ChemGrout CG500 – Soil Anchoring
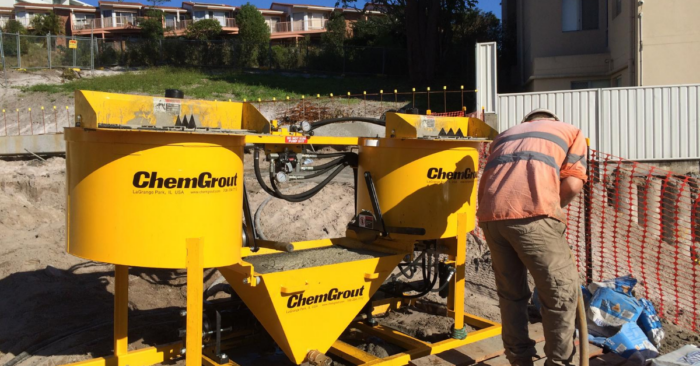
High-Performance Soil Anchoring: Fusion Civil Partners with CGS Equipment for Port Stephens Retail Project
Project Background
Fusion Civil specialises in retaining walls, ground anchors, shotcrete, soil anchoring, and reinforced earth walls. The Port Stephens Council engaged Fusion to undertake a significant civil development project which included new retail sites, a 3,457-square-metre shopping centre and a basement car park with capacity for 180 vehicles. Fusion approached CGS Equipment seeking a solution for their requirement – a grout plant capable of mixing and pumping at high pressures and efficiently reinforcing >200 soil anchors.
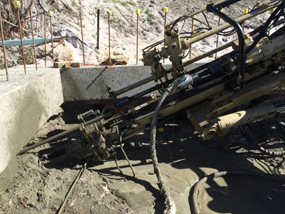
The CGS Equipment Solution: Chemgrout CG500 High Pressure Series
Based on Fusion’s requirements, CGS Equipment recommended the Chemgrout CG500 High Pressure Series. This powerful grout plant includes a double-acting positive displacement plunger pump capable of handling high pressures up to 2,000 psi (137 bar), making it ideal for soil and rock anchoring applications.
Drilling teams installed each anchor using a spinning head mounted on the drill rig, followed by grout injection. After curing, the anchors were tensioned using hydraulic power packs to secure their placement. The reinforced soil anchors limit wall deformation during the construction phase and are critical to supporting the surrounding infrastructure.
Working alongside an Ingersoll Rand ECM660 drill rig, the CG500 enabled the crew to install 8–9 anchors daily, spaced at 2.2 metres. Each anchor, a 35mm galvanised hollow bar in 3m sections, was installed to a depth of 12m using low-viscosity grout as the drilling fluid.
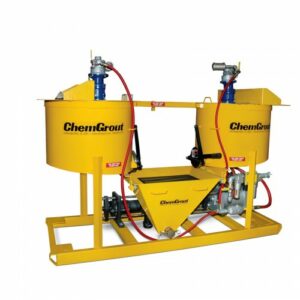
Key Features and Benefits
The CG500’s twin tank setup was key to efficiency. Operators switched from low-viscosity to higher-density mix before the final rod was inserted on each anchor. This flexibility significantly improved the efficiency of the project team whilst also improving bond performance and delivering a stronger anchor.
The hopper’s fine mesh screen filtered out packaging debris and clumps, protecting the pump and maintaining consistent output. The hydraulic paddle controls allowed fine adjustments to mixing speed, minimising splashing when adding dry product.
Reversible paddles delivered fast, homogenous grout mixes. Operators reversed mixing direction to quickly shear and blend cementitious materials into a smooth, pump-ready mixture. This efficient system reduced downtime, labour, and material waste across the site.
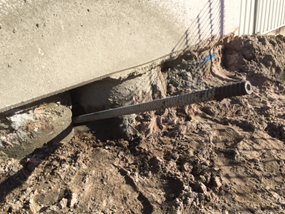
Let’s Talk Grouting Solutions
CGS Equipment supplies high-performance grout pumps and mixers. We also offer a wide range of equipment for all things Concrete, Grout and Screed.
To learn more about the Chemgrout CG500 High Pressure Series, speak with our expert team today.
1300 581 984
sales@cgsequipment.com.au