What Is Volumetric Concrete Mixing?
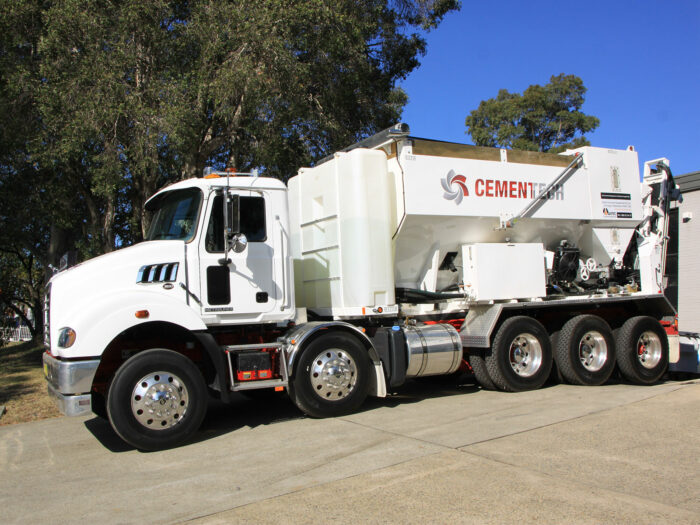
Volumetric concrete mixing is a method of preparing concrete in which raw materials like sand, gravel, cement, water, and other required admixtures are mixed together in a specific ratio as needed. Rather than being pre-mixed at a batch plant and delivered to the site, volumetric mixing is carried out on the worksite. This process requires a volumetric concrete mixer, which is a mobile truck that contains separate compartments for each of the raw materials.
Benefits of volumetric concrete mixing
- Control: Mix specifications, time and production. Make adjustments at any time.
- Quality: Fresh concrete with maximum strength and workability every time.
- Speed: Streamline production and turn projects around faster with less downtime and quick clean-up.
- Reliability: Materials are stored dry in separate compartments, so there is no risk of setting.
- Adaptability: Suitable for short pours, readymix delivery, civil applications, mining, precast, shotcrete/gunite and specialty concrete including fast setting, coloured and pervious. Great for producing concrete in remote locations.
How volumetric concrete mixing works
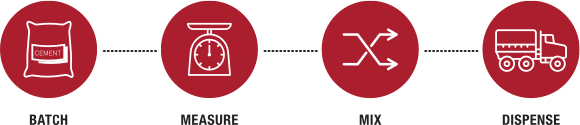
Volumetric technology makes it easy. Load your materials in separate compartments, and you’re ready to go. In fact, you can be ready to pour in a matter of seconds.
For example, Cemen Tech volumetric concrete mixers are calibrated by weight, so there’s no guesswork. The operator just needs to select from a range of mix designs, and then materials are dispensed via the linked dual auger system and conveyor belt into the mixing auger.
Just 10 seconds later, materials are mixed and ready to pour.
Cleanup is easy, too. The mixing auger’s cleanout takes less than 5 minutes. Then, it’s on to the next job, which can require a different mix of design and quantity until all the materials have been used.
5 Volumetric Concrete Mixer Myths – Busted!
Below are some of the most common myths and misconceptions so you can confidently move forward with your project.
Myth #1: Volumetric concrete mixing is a new and unproven technology
Volumetric concrete mixing has been around since the early 60s, with the patent granted for Concrete-Mobile in 1965. It didn’t take long for consumers to recognise this highly effective and efficient method, with more than 2,500 Concrete-Mobiles produced by 1980, which shot up to 10,000 by 2000.
Flash forward to today, and volumetric concrete in all of its forms is used in every state in the U.S. and over half of the countries in the world. It is even used by the U.S. Military, along with many State and Local Departments worldwide.
Myth #2: Volumetric concrete mixers cannot match the accuracy and consistency of a batch plant
Volumetric Concrete Mixers have the same tolerance as typical batch plants on all materials. While there are more restrictions on ready mix as water-cement occurs at the plant, there is not the same restrictions at the job site, and Volumetric Mixers often allow for more control over proportioning and mixing. Our Volumetric Concrete Mixers have ACI 304.6R “Guide for the Use of Volumetric-Measuring” VMMB (NRMCA) approval and specification.
Myth #3: Volumetric concrete mixers don’t produce “good concrete” (e.g. not enough mix time)
Our rich history of happy customers has revealed many examples of high-quality concrete, including:
- Bridge deck overlays
- Airport runway repairs
- Structural elements
- Pool builders, Soil retention
- Pervious concrete
- Lightweight concrete by foam and lightweight aggregates
Myth #4: Volumetric concrete mixers cannot handle large production pours or projects
On the contrary, a single piece of equipment can be reloaded at the job site – meaning no time or fuel is wasted in transit. Volumetric equipment is capable of production rates in excess of 69 cubic metres per hour, and we have seen many examples of large-scale projects completed with volumetric machines. The most common volumetric model on the market today will produce .76 cubic metre of concrete per minute.
Myth #5: Volumetric mixers are too complex to operate and have too long a learning curve
Like on any other jobsite, proper training of operators is a must when using this equipment. An operator of a volumetric mixer must have more training than a typical barrel mixer operator – “batch plant on wheels”. We offer extensive training in the operation, maintenance and calibration of their equipment, and soon, the typical “day-to-day” operation becomes straight-forward and repeatable.
Volumetric Concrete Mixers offer a host of advantages, including on-site mixing flexibility, precise control over concrete composition, and significant cost savings by reducing waste. These benefits make them a valuable asset for various construction projects. However, it is important to weigh these benefits against potential drawbacks, such as the initial investment cost and the need for skilled operators.
By carefully considering the specific needs of your project and the long-term advantages, you can determine whether a volumetric concrete mixer is the right choice for your construction operations.
For more information or to know more about our range of volumetric concrete mixers, feel free to contact CGS Equipment today.