Servicing & Maintenance Tips for Concrete and Grout Mixers and Pumps
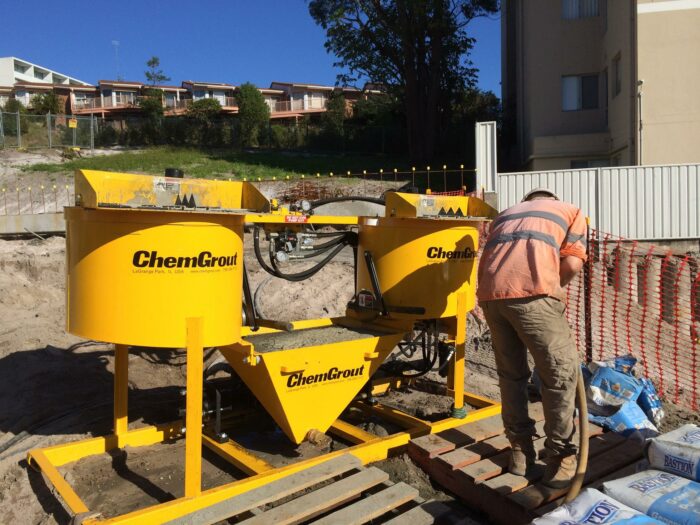
Concrete and grout mixers and pumps are essential machines on any worksite. They’re designed for heavy-duty endurance work, mixing cement, sand, grout mixture and aggregate for extended periods. Their reliability and toughness often mean they can be overlooked in the maintenance cycle, but material buildup, corrosion, friction and wear can all reduce the lifespan, efficiency, and overall condition of the mixer or pump.
Regularly maintaining your equipment is crucial and comes with a range of benefits: it increases its longevity, improves the safety of operation, makes it more efficient, and contributes to cost savings on part replacement and other repairs.
In this article we explore maintenance tips and recommendations for your worksite’s concrete and grout mixers and pumps.
Why Servicing Your Mixers and Pumps is Important
CGS Equipment’s concrete and grout equipment is designed to be tough. However, regular servicing and preventative maintenance remain critical in ensuring these machines remain operating at full capacity for many years.
Servicing your mixers and pumps helps to prevent breakdowns by identifying the marks of damage before they cause issues. This extends the equipment’s life, as well as the length of time between replacing worn-out components. Regular servicing is also important for ensuring the machine is working efficiently and safely, producing consistent concrete or grout output, and delivering the highes quality material. Together, these factors deliver what is most important, satisfied customers.
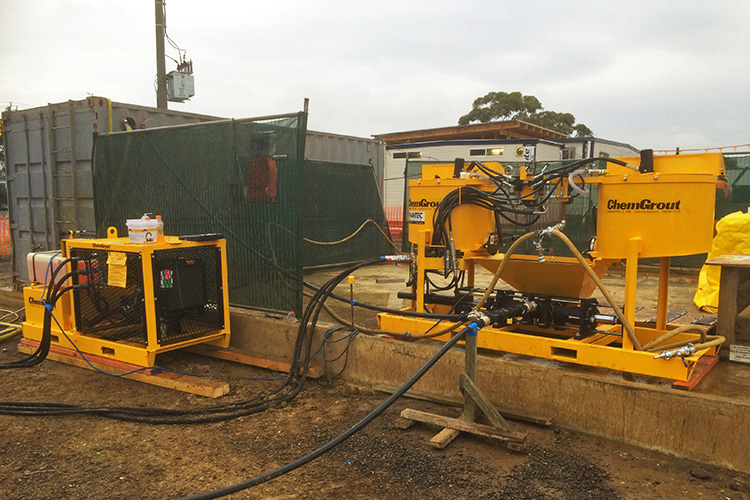
What are the typical requirements for properly maintaining your equipment?
Training
Before using your equipment, you must ensure that all operators are fully trained. A trained operator holds the knowledge required to use the equipment correctly and avoid any errors and damag caused by human mistake.
Operator error is one of the most common causes of damage to a machine and is easily avoidable with the right training upfront.
Daily Maintenance Checklist
Maintenance schedules for different machines depend a variety of factors including model type, the length of time they are used each day, the material being mixed and pumped and the worksite conditions. However, there are basic maintenance tasks that should be performed every single day after use.
The mixer or pump should be properly cleaned after every use to ensure no material build up and avoid potential damage to the machine. This simple step will prevent a large proportion of the potential issues CGS Equipment repairs frequently. It is vital to wash the equipment with water (and a cleaning solution where appropriate) and to pay close attention to any cement powder, concrete or grout mixture that has worked its way into connections or components.
- Before and after use, the operator should inspect components for signs of wear and tear, particularily items prone to friction and pressure including bearings, seals, pistons, mixing blades, rotors & stators.
- The operator should check the entire machine for loose connections and tighten them back up, if necessary. The heavy vibrations and mixing motion can shake components loose over time, so always assess the machine’s structural integrity after each day’s work.
- Moving parts should be inspected and if required, lubricated with specialised oil or grease. This is one of the best ways to prevent unnecessary damage to the belts, the engine, and gearbox of the machine.
- All fluid levels should be checked and topped up if required.
Finally, the equipment should always be used within the manufacturers recommended guidelines. Operating outside of these guidelines gives rise to a number of risks including unsafe operation and voiding any manufacturer warranty.
Periodic Servicing and Maintenance Tasks
While the above checks should be conducted daily, several other tasks only need to be done periodically. The frequency of maintenance will mainly depend on how many hours a day the mixer or pump is operating, the material used and work site conditions.
A regular maintenance program is vital for your equipment and will ensure it continues to operate long into the future.
During a regular maintenance check, a thorough inspection is undertaken and any worn-out components that display signs of wear and tear are replaced. Malfunctions often arise from a damaged component that is pushed to failure.
Troubleshooting Common Issues with Your Concrete and Grout Mixer or Pump
When conducting your inspections, you may find that your machine’s operations are not meeting your expectations. This can be a result of natural wear and tear or the need to deep clean and properly lubricate working components. Construction sites are full of debris, dirt, dust and other contaminants and over time they can work their way from the exterior to the interior.
Examples of common issues include unusual noises, which often arise due to friction from worn components and insufficient lubrication. Listen to where the noise is coming from and attend to the grinding components accordingly.
Uneven mixing is usually the result of misaligned blades or an uneven balance. Always ensure a level platform, and check that the mixing blades are evenly aligned to make sure that materials in the mixing drum are always evenly dispersed and properly mixed together.
Mechanical failures arise from wear and tear and operational damage over time. Check for dents, cracks, and signs of leakage in the inside of the drum and the engine interior, but also on the machine’s casing.
Quick fixes include lubricating and greasing components, cleaning gravel and grit from workings, and realigning blades, if necessary. Issues with the motor and electrical workings, require the assistance of a professional.

Professional Servicing vs DIY Maintenance
CGS Equipment strongly recommends that its customers undertake a regular professional maintenance program. A routine maintenance schedule complements the regular checks performed by the operator and can be planned in advance to reduce any unexpected down time.
Benefits of professional mixer and pump servicing include:
+ Professional knowledge: Trained technicians have encyclopaedic knowledge of mixer and pump maintenance.
+ Access to parts and tools: Professional servicing will have all required parts and tools already on hand—no need for you to source them yourself.
+ Saving time: Your own personnel can attend to other tasks on the construction site rather than wasting time trying to work out how to open up the machine.
+ Reduced risk of further damage: There is always the risk of accidentally damaging the mixer further if you attempt to fix it without the assistance of a professional.
+ Genuine parts: The use of genuine parts is essential for optimising machine performance and not running the risk of voiding any manufacturer warranty.
+ Warranty: CGS Equipment provides a warranty for all of its maintenance and service work.
Operate at Peak Performance, Minimise Downtime & Maximise Productivity
The benefits of regular concrete or grout equipment maintenance cannot be overstated. By taking just a few active steps, you can ensure that your mixer or pump operates at peak performance as its manufacturers intended. Properly training your operator will significantly reduce the potential for serious damage. By anticipating malfunctions and breakdowns, you can also minimise downtime, particularly important in the construction industry where lost time literally means lost money.
Don’t take the risk of having your machine break down. Schedule professional servicing or training with CGS Equipment to keep your concrete and grout mixing equipment operating at its very best. Call or email our expert team today to learn more about maintenance and upkeep or to discuss the optimal maintenance schedule for you and your machinery.