Concrete, Grout and Screed Equipment Safety Tips Every Operator Should Know
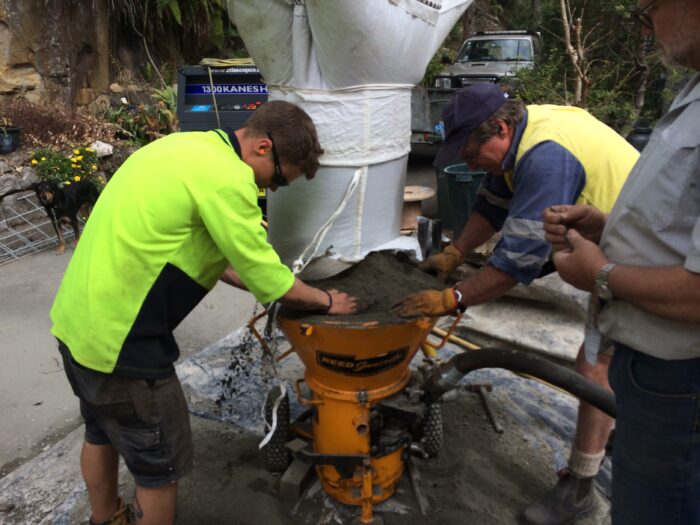
Safety in equipment operation is crucial for every worker to understand. The potential risks and consequences of neglecting safety practices range from a job done poorly to serious and even permanent injury.
Concreting, grouting, and screeding are precise tasks that can be physically demanding. They often require long hours spent mixing, pouring, and levelling to achieve a perfect finish. Continually refreshing your safety knowledge is crucial to maintaining the safety of the job site but also optimising the efficiency and output of your equipment.
Join us as we explore essential safety tips for operators, whether you’re an experienced worker updating your skills, new on-site, or researching before investing in new equipment.
Understanding the Basics of Equipment Safety
Ensuring the safe and effective operation of concrete, grout, and screed equipment begins with understanding the tools used on-site. A huge range of equipment and tools exist to assist operators. These range from smaller hand-held tools (e.g. screw mixers, screeders) through to large pieces of machinery (e.g. pumps, automatic mixers).
Each piece of equipment must be operated according to the manufacturer’s instructions. Further, there are general safety precautions applicable to all equipment. Understanding your equipment is a vital first step. A sure way to achieve this is to ensure all operators are properly trained.
The Importance of Regular Training
Training is a must-have requirement before using any equipment on-site. Proper training provides the operator with the confidence and knowledge to properly use the equipment, whilst ensuring working practices are safe and in accordance with the manufacturer’s requirements. A poorly trained operator not only poses a risk to the safety of the job site, it also reduces the output of your equipment (and therefore return on investment) and the useful working life.
Ensure that only properly trained operators use the equipment. If necessary, they must also hold relevant certifications and have a comprehensive understanding of the safety protocols required to operate the equipment safely.
Pre-Operation Safety Checks
Before operating your machinery, there are several safety checks you must complete before every use. First, visually inspect the equipment and its componentry for signs of wear and tear, damage or malfunction. Parts that are damaged or worn will significantly reduce the performance of your equipment and may increase the potential dangers to the operator.
Next, verify fluid and grease levels , including hydraulic oil, engine oil, fuel and coolant. It is vital for the extended life of your equipment that it remains properly lubricated.
Inspect all electrical connections, cables, batteries and powerboards for signs of wear or damage. Faulty wiring can lead to equipment failure or electrical hazards.
Look for any signs of leaks such as fluid markings on the ground or equipment. In particular, inspect the areas around hoses & fittings, seals, cylinders, pumps, bearings, joints etc.
Ensure all safety equipment, including personal protective equipment (PPE) is in good working condition without any damage or compromised components.
Finally, conduct a pre-job trial of the equipment including starting the equipment and if possible, pumping a small amount of material through the machine to confirm everything is in proper working order and the output quality is acceptable.
Best practice would include maintaining a log of all pre-start inspections for your equipment.
Wear Appropriate Personal Protective Equipment (PPE)
It is important to wear appropriate personal protective equipment while operating concrete, screed and grout equipment. This includes a mask to avoid inhaling cement powder when mixing and protective gear when working with wet concrete.
Before starting work, inspect all PPE for damage and ensure it fits correctly. Supervisors should provide training on the proper use, storage, and maintenance of PPE, reinforcing workplace safety while reducing unnecessary equipment replacements.
Always remain vigilant and ensure that all workers understand the importance of wearing PPE at the correct times, even if a job only takes a few minutes.
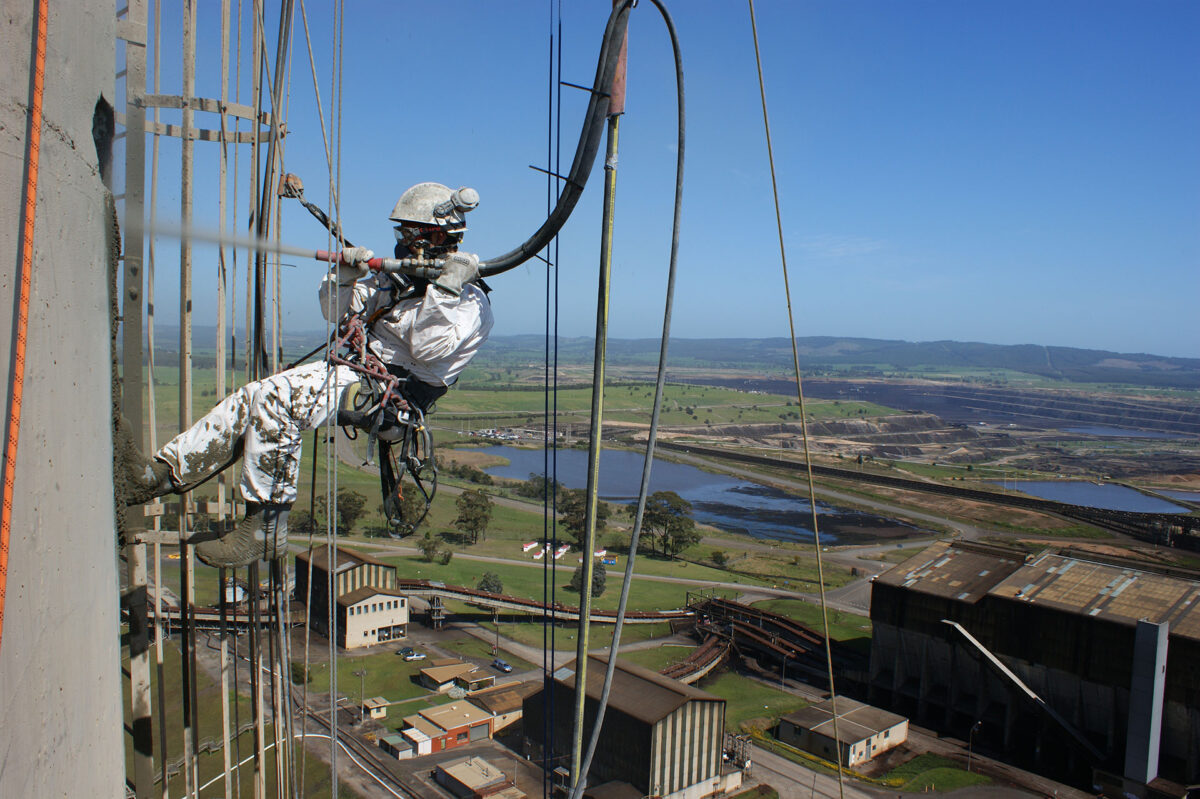
How to Ensure Safe Operation
Follow all manufacturer and industry guidelines for the operation of mixers, pumps, and other equipment. The operating parameters provided by the manufacturer are designed to maximise the useful life of your equipment, maintain a consistently high level of output quality and minimise any potential dangers whilst the equipment is in use.
Ensure that the operator abides by these standards at all times, even when job deadlines are looming or complacency sets in towards the end of the workday. Operating your equipment outside of these guidelines will very likely affect the warranty of the machine and any insurance claim in the event of an accident.
Reiterate that wearing PPE is as important to the job as completing the work correctly.
Job Site Safety and Organisation
The site manager plays a vital role in maintaining safety on site. It is their responsibility to ensure the site is well organised and safe. Site safety plans should be clearly communicated to all attendees. Workers should maintain a clean and organised job site at all times.
Remove tripping hazards and make sure there is a clear path through the site with easy access to safety equipment. Ensure that materials are stored and disposed of correctly.
If necessary, consider implementing traffic control measures to prevent collisions between workers moving equipment. Designate a specific area for storing equipment and ensure that all workers are aware of the layout of the job site, any potential hazards, and the proper place for equipment and materials.
The site should be frequently monitored and reviewed to ensure safety standards are upheld.
Post-Operation Safety
Similar to pre-start checks, post-work procedures must be performed every day. At the end of each workday, thoroughly clean your equipment, especially in areas in direct contact with material. Remove any debris, dirt, or dust and perform another visual inspection of the equipment post-clean. Properly cleaning your equipment is an easy-to-do task that is most often overlooked by operators, often resulting in serious (and expensive) damage.
Identify any parts that require maintenance or replacement.
If in doubt, always refer to equipment safety manuals and guidelines as well as any other manufacturer information to stay current on best practices.
Ensure that all workers are aware of proper incident reporting procedures and form a culture where they are not hesitant to do so. This means making sure concerns are heard and issues are promptly addressed.
Keep Up Regular Maintenance
A regular maintenance schedule must be implemented for your equipment. CGS strongly recommends using a trusted equipment servicing business with intimate knowledge of your machine. The frequency of maintenance will depend on the equipment and how often and for how long it is used.
If you are using high quality equipment, a regular maintenance schedule will keep your machine operating at peak performance for decades.
Continuous Improvement
With other supervisors, site managers, and foremen, regularly review and update your site’s safety policies and procedures so that they remain relevant and up to date. Encourage feedback and suggestions from the operators who use the equipment regularly.
Be sure to implement changes and improvements based on feedback and fill any knowledge and safety gaps with training if required. Always reiterate the importance of following safety protocols and the specifications of the machine. A moment of laxity can result in permanent injury.
Common Safety Mistakes and How to Avoid Them
- No workplace culture supporting safety and continuous education
- No operator training
- No pre-start checks completed and no record keeping of maintenance items
- Improper use of the equipment, including using it outside of the manufacturer’s specifications
- No monitoring of the equipment whilst in operation
- No post-job checks
- Poor or no cleaning after use
- Not wearing appropriate PPE
- No continuous education and training provided to operators
- Operating on an unsafe work site
These mistakes are quick and/or easy to rectify but make an enormous difference to the safety of your equipment and the work site. Addressing these mistakes will also maximise the performance of your equipment.
CGS Equipment: Your Partner in Job Safety
For further advice on your concrete, grout and screed equipment needs, from the right servicing schedule to optimising performance, speak to one of the expert team at CGS Equipment. With extensive experience in supplying equipment for a wide range of situations, our team has the solution for you.
We offer on-site and in-house training, servicing and maintenance on all types of machinery and equipment, and can provide advice and know-how to provide you with all the solutions you need. Get in touch with us today to let us help you with all things equipment safety.